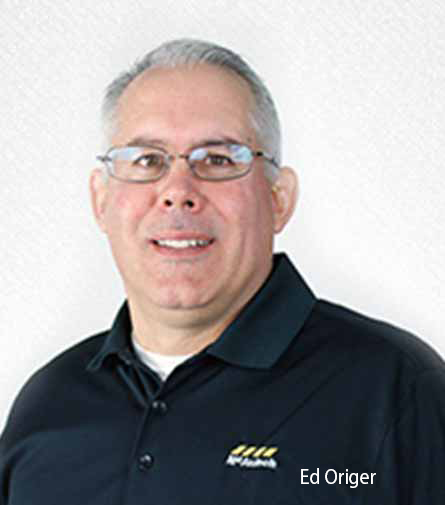
The story of Dwayne McAninch, founder of McAninch Corporation, has an inspiring edge in the earthmoving business. As a kid, Dwayne was fascinated by Bulldozers and Heavy earthmoving equipment and quickly learned how to operate them. After graduating from high school in 1954, Dwayne—deciding to follow his father’s footsteps—bought his first Bulldozer, a used International TD14 and started a small earthmoving business. In 1962, he bought his first new D-7 CAT Bulldozer. In 1967, determined to revolutionize the construction industry, Dwayne founded McAninch Corporation, a firm dedicated to offering innovative services to the mass earthmoving and construction industry. In the 1970s and early 1980s, the company was involved in creating a ready-mix concrete and paving business. While Dwayne was successful in this venture, he wanted to do more in the grading industry. Since then he has grown the company into a multi-million-dollar business that specializes in both large-scale mobilizations of equipment for mass grading work as well as a variety of smaller projects. McAninch’s cutting-edge services include everything from earthmoving and grading to GPS topomapping, value engineering design assistance, and site management. Ed Origer, chief operating officer of McAninch, says, “Today, we are among Iowa’s largest earthmoving and underground utility contractors. We are nationally recognized as one of the most technologically advanced earthmoving contractors.”
McAninch is, in fact, is one of the first contractor in the U.S. to adopt GPS machine guidance. “For decades, equipment operators took their instructions from grade stakes in the ground that had to be moved and reset as the work unfolded,” adds Origer. Not only was the entire process time-consuming, but it also led to inaccuracies in topographic information.
Thus, when Caterpillar and the major supplier of GPS instruments, Trimble Navigation, established a joint venture CTCT and co-developed a groundbreaking GPS technology designed to automate the repetitive earthmoving business, McAninch took it upon itself to assist the business in perfecting the equipment in the field.
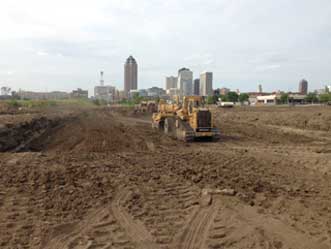
Eager to explore the possibilities, the McAninch team helped the joint venture retool designs and test prototypes on McAninch’s scrapers, dozers, and excavators in the field. After analyzing the GPS application’s use on earthmoving projects, McAninch was instrumental in educating the construction industry on the benefits of GPS-based digital earthmoving and grading controls. Today, McAninch’s fleet of equipment use the GPS technology, and it helps them improve job efficiency, accuracy, and quality.
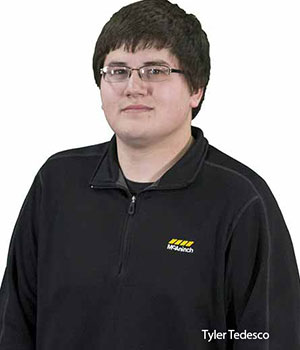
As a result, supervisors and foremen no longer have to reset stakes, instead, they can concentrate on monitoring the work, haul routes, and cycle times. The real-time information offered by GPS-enabled equipment allows for more effective monitoring of the construction work, detailed and accurate management of individual pieces of equipment, and more precise cost analysis. Moreover, earthmoving operations are safer because less time is spent on the ground and fewer people are involved.
When it comes to topographic surveying and mapping, McAninch uses drones. These devices enable field operators to capture detailed site maps, including contours and terrain, in a fraction of the time and cost of traditional methods. Darin Eckels, project manager at McAninch, informs, “We specifically use sense Fly’seBee X fixed-wing drone. The GPS-guidance technology integrated with the drone has streamlined and simplified the surveying process to a great extent.”
To further exemplify the benefits, Eckels cites a case in point involving a rock quarry. McAninch was removing some overburden for the client, and there were a lot of high walls and safety restrictions. To that end, McAninch was able to use the sense Fly eBee X fixed-wing drone to capture the topography. “The data from the drone was more accurate than the data that a surveyor gets from a person holding a survey rod in the field. The GPS technology has fine-tuned our equipment’s ability to topo-map sites and helped our project managers and estimators have the most accurate information,” asserts Tyler Tedesco, GPS manager at McAninch.
Besides, McAninch employs a unique approach to project design and fulfillment. The firm partners with public and private-sector clients to eliminate constraints and identify cost-saving opportunities wherever possible. The company strongly believes that the key to a successful project is early collaboration and open communication with the McAninch team. To date, McAninch has partnered with some of the biggest companies and helped them with their mass earthmoving, underground utilities, and value engineering needs. For the days ahead, McAninch is hoping for a structured growth. At the same time, the organization is also striving to be a one-stop-shop for earthmoving and underground utilities projects. “Bigger isn’t always better; better is better. And, that’s what we want, to be the best that we can be,” concludes Origer.